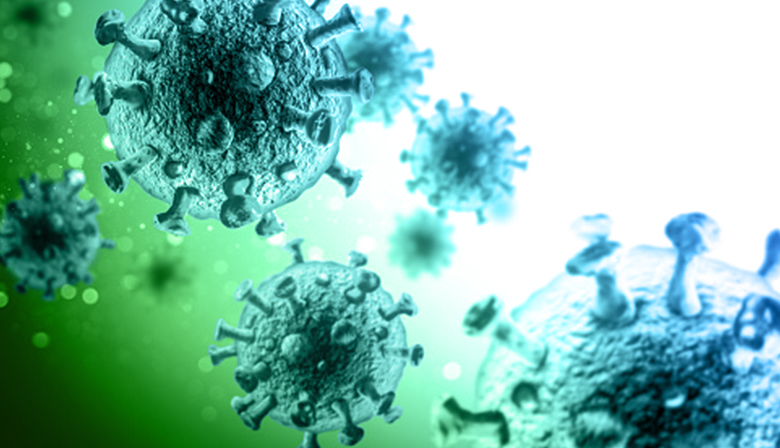
In late 2019, our team was finalizing plans to begin a first-of-its-kind groundwater remediation project at a former refinery. The goal was to inject contaminant-degrading microbes (to be grown in a laboratory in Ontario, Canada) into impacted groundwater to biodegrade historic benzene. The process, known as enhanced in-situ biodegradation (EISB), has a long history of success. Still, the particular target contaminant and the site conditions posed a Spring 2020 challenge for the team.
Then came a killer global pandemic.
As our team was working to implement their plan, the COVID-19 pandemic reached the U.S. In early March 2020, COVID-19 cases were confirmed in counties surrounding the facility. The total number of cases soon began to rise locally, and it quickly became clear that new policies and restrictions were going to be put in place at a state and local level.
A mandatory safety stand-down was held to discuss the new safety protocols that were being developed to respond to the situation and mitigate risks to employees. Daily meetings between facility management and safety teams were being conducted, and a business continuity/contingency plan was formalized based on guidance by the CDC to protect workers, identify vulnerabilities, and limit impacts on the project. These protocols were explicitly developed to be fluid, to allow for adjustments to be made as new information was learned about the virus, its transmission, and successful prevention. Early protocols directed employees to:
- Stay home if feeling sick or exhibiting any symptoms such as a fever or coughing
- Wash hands frequently using soap and water
- Use alcohol-based hand sanitizer frequently as recommended;
- Avoid touching their face
- Wear nitrile gloves at all times when handling laboratory coolers, bottle ware, and rental equipment;
- Practice social distancing with no more than ten persons gathered together at a time;
- Maintain six feet between personnel;
- Discontinue lunch gatherings;
- Employ teleconferencing for meetings;
- Increase the cleaning frequency established with the contracted office cleaning service; and
- Perform twice daily disinfection of all hard surfaces in high-use areas.
It should be noted that the national guidance at the time regarding the use of face masks was that they are limited to medical personnel, first responders, and those who felt sick.
Within a week of the mandatory safety stand-down, the facility was under a state-issued shelter-in-place mandate. Work at the facility paused while projects were evaluated to determine if they met guidelines for essential work. The EISB injection project was deemed essential, allowing personnel to continue working without breaking the shelter-in-place rules.
Construction of the EISB manifold, wellhead connections, and piping continued as planned, though the procurement of additional required personal protective equipment (PPE) was sometimes hampered by a worldwide spike in demand and the preferential shipment of masks and nitrile gloves to medical personnel and first responders.
_____________________________________________________________________________
The border between Canada and the United States was beginning to close, complicating the receipt of the microbial cultures needed for the injections. The first shipment got stuck at the carrier’s U.S. warehouse due to shipping disruptions. Still, fortunately, the lab was able to prepare and send a replacement shipment, which arrived without incident.
Injections began in late April and continued through June, alongside daily safety meetings reminding employees of the new virus-related safety protocols. Employees soon adjusted to the “new normal” of working under a cloud of COVID-19, which included:
- Daily temperature checks and completing a medical screening questionnaire before working
- Donning their face masks at all times, in addition to regular PPE usage
- Social distancing while working
- Gathering for lunches was prohibited. This meant that lunch tables and other traditional gathering locations were now off-limits
- Holding all meetings outdoors
- Specialized cleaning protocols were implemented, using approved cleaners and sanitizers, which included but were not limited to:
- Work vehicles and trailers
- Clipboards, pens, phones
- All injection and monitoring equipment
COVID-19-related tasks took more time than usual and were not always comfortable. As the weather warmed, heavy face masks were replaced with lighter surgical masks to improve comfort, and additional breaks were planned to allow for rest and rehydration.
Injections were completed in June 2020, and all preliminary data suggests that they will be successful. This project had to overcome:
- The geography of technical experts located across the U.S., working together to develop a cutting-edge, first-of-its-kind EISB injection event at this type of location
- Site temperatures that ranged from freezing to over 90 degrees, and site conditions with multiple challenges, including simultaneous operations from other projects
- International colleagues with logistical challenges that required constant communication and coordination in order to deliver the necessary microbes at the right times
- Many recognized hazards that exist with this kind of work under the best of circumstances
- A deadly viral pandemic
Thanks to the communication and flexibility of the team, along with a well-established safety culture before the onset of the virus, in the end, there were zero injuries, illnesses, or safety incidents during the duration of this project.